DISCLAIMER
The information presented here is meant to be used as an educational asset for the Space community, both for commercial, non-commercial entities and individual actors; the use case has been generated through IENAI’s GO™, an intuitive thruster design and mission analysis tool on the cloud, which is open-access and free-to-use for the community. External data and assets have been gathered in good-will and, to the best of our knowledge, are accurate, but are not intended to replace official information released by companies, institutions, or other stakeholders. All author’s rights have been reserved; reproductions shown here are intended with educational uses only.
The present use case is intended to showcase the capabilities of IENAI’s ATHENA™ electrospray thrusters in an application for constellation deployment of OneWeb. The ultra-high efficiency and uniquely scalable nature of the thruster allows for a reduced and customizable form factor, tailored to the requirements and limitations of the satellite platform and the specific maneuvers for which it is intended. This application has not been sponsored by OneWeb in any way.
TL;DR
- ATHENA™ thrusters perform similarly to current OneWeb thrusters while saving mass and reducing costs.
- Costs savings for the constellation are around 8M$, taking into account only the propellant savings!
- The propulsion system uses 9 kg of propellant for 3 different maneuvers: Orbit phasing, Orbit transfer and Deorbit; saving over 30% of the propellant projected for the original mission.
MOTIVATION
OneWeb is presently building a communications network through a satellite constellation operating at 1,200km altitude, with a planned fleet of 648 satellites, out of which 428 satellites have already been launched and remain operational. The constellation will be completed in the next 6 launches, if they hold the rate of 34-36 satellites per launch; although recent geopolitical conflicts may challenge the company’s timeframe or its access to its current propulsion system, the SPT-50M, produced by EDB Fakel. A second generation of OneWeb is already being considered for the replenishment phase of the constellation, with expanded capabilities for users; industry rumors point to a re-engineering of the propulsion system for this second generation.
OneWeb uses Airbus’ ARROW platform, which can be designed for a variety of space applications, including in-orbit demonstrators and other complex missions with sophisticated payloads. The platform is uniquely suited for a mega constellation configuration such as OneWeb’s, with this application being one of its main design drivers. ARROW falls in the 200kg satellite class and provides a slot for payload mass up to 100 kg. The solar panels provide a dedicated orbit average power (OAP) of 210 W for the payload. Designed to provide a minimum lifetime of 5 years at a 1200-km circular polar orbit. ARROW also targets a high reliability of 0.96 over its 5 year mission. In terms of maneuvering, it has been designed to be compliant with post-mission disposal regulations, saving propellant during the mission to allow for deorbiting the satellite at the end of its operational lifetime. Propulsive phases are currently carried out by a Xenon hall-effect thruster (HET), the aforementioned SPT-50M.
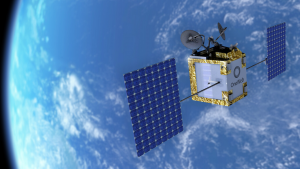
The deployment of the constellation has been performed over 13 batches, starting in February 2019 and with the last batch hauled by Soyuz taking place in February 2022; the sixth OneWeb batch is analyzed in this case study. This batch was launched on April 25, 2021, and consisted of 36 OneWeb satellites delivered at an altitude of 440 kilometers by the Soyuz rocket. Batch 6 was selected in this use case for its excellent deployment, where all satellites successfully raised their orbits and are now operational. The deployment maneuver consists of a 760 km orbit raising with a small change in inclination, after which orbit maintenance maneuvers are carried out constantly through the mission, ending with the final deorbit burn. Note that one satellite in the constellation, from Batch 8, was already deorbited, with a second satellite currently deorbiting, but neither had performed the orbit raising maneuver; thus the deorbiting strategy from One Web is currently unknown.

The present study aims to provide an example of the capabilities of the platform under the assumption that IENAI’s ATHENA™ thruster has replaced the SPT-50M as the main propulsion system. The reasons behind the reengineering of the propulsion system can be many: from cost or logistics-based, to purely performance based or due to systems-engineering concerns (HETs are widely known to have non-negligible thermal management requirements, for example). Furthermore, presently, the supply chain of these systems, and of propellants such as Xenon or Krypton, may also be endangered under the current world climate, and new technologies can be counted on to pick up the slack if dependency on non-EU countries is to be reduced.
Thus the quick evaluation of new propulsion systems for the next generation of One Web can be an asset for mission designers and systems engineers in order to address current challenges both for existing and future versions of the constellation. ATHENA™ can provide comparable performances in terms of maneuvering time while saving propellant mass and overall volume footprint, allowing for larger payload mass or potentially reducing the volume of the spacecraft, which may allow for larger batches being ferried in single launches. Furthermore, ATHENA™ runs at temperatures comparable to other spacecraft electronics and thus no ad-hoc thermal management is required!
This use case presents the “inverse propulsion problem”, as solved through IENAI’s GO™ tool, obtaining an optimal configuration of the ATHENA™ thruster for the mission’s requirements, during a theoretical redesign phase. As a reference, a comparison for the specifications of the SPT-50M and the ATHENA baseline
PARAMS | SPT-50M | ATHENA |
---|---|---|
Thrust [mN] | 14.8 | 4.3 |
Specific Impulse [s] | 930 | 1650 |
Dry Mass [kg] | 1.3 (minus PPU and deposit) | 2.4 (including PPU and deposit) |
Thruster power [W] | 300 | 94 |
SIMULATING IN GO™
As shown in Figure 2, the total deployment time for Batch 6 was approximately 6 months, performing an orbit raising to 1,200 km altitude with small stops for collision avoidance or slot placement. For comparison purposes, an average duty cycle of 31.3% is deduced for the propulsion system, considering the maneuver in Figure 2 (total deployment time 180 days), the 210W OAP from the ARROW platform and the nominal thrust specified in EDB Fakel’s datasheet of the SPT-50M (14.8 mN). Assuming a PPU efficiency of 73.3% based on the state of the art for a HET of 300 W total power, the resulting compounded OAP fraction available for the propulsion system is about 94 W.
The OneWeb mission presented here can be easily translated into the required input parameters in GO™. The first step will be to define these parameters in the Configuration view for a “Custom” platform. This section allows the user to define the parameters of the platform, thruster envelope and initial orbit; the following table shows the used platform specifications. The mass, solar panels, and launcher were input as closely as possible to publicly disclosed data from OneWeb.
Mass | Platform | Solar panels | Power | Limit thruster mass |
---|---|---|---|---|
148 kg | Custom | 13,068 cm2 | 210 W | No |
The worst case scenario in terms of ΔV is chosen to derive the most stringent requirements for the propulsion system. It’s assumed the 36 satellites compose an equally-spaced, coplanar constellation; thus, a satellite placed every 10º in true anomaly. The worst case will be the satellite placed at 180º from the injection phase. For this scenario, the following maneuvers were simulated:
- In-plane phasing with RAAN compensation (slot placement).
- Orbit transfer to 1200 kms (deployment).
- Deorbit (after operational lifetime)
MISSION CONFIGURATION
Once the platform configuration from Table 2 has been implemented, we will fill out the thruster envelope: a 96W average power is used for the thruster, being the closest feasible option to the allowed OAP fraction of 94W, estimated above. The total mass of the thruster is left unconstrained, in the absence of a disclosed specific limit for the amount of propellant, which, in any case, will be less than that consumed by the Hall thruster due to the higher Isp of ATHENA™.
Once these parameters are defined, we proceed to select the initial orbit. In this step, the user has two options: Custom orbit or Launcher selection (provided by our colleagues at Precious Payload!). In this particular case, we selected a Custom orbit of 440 km altitude (circular) and 87º of inclination, according to the initial point in Figure 3. Once the launcher is selected, the configuration is saved by clicking on the “Save” button, after which we are redirected to the maneuvers scenario view.
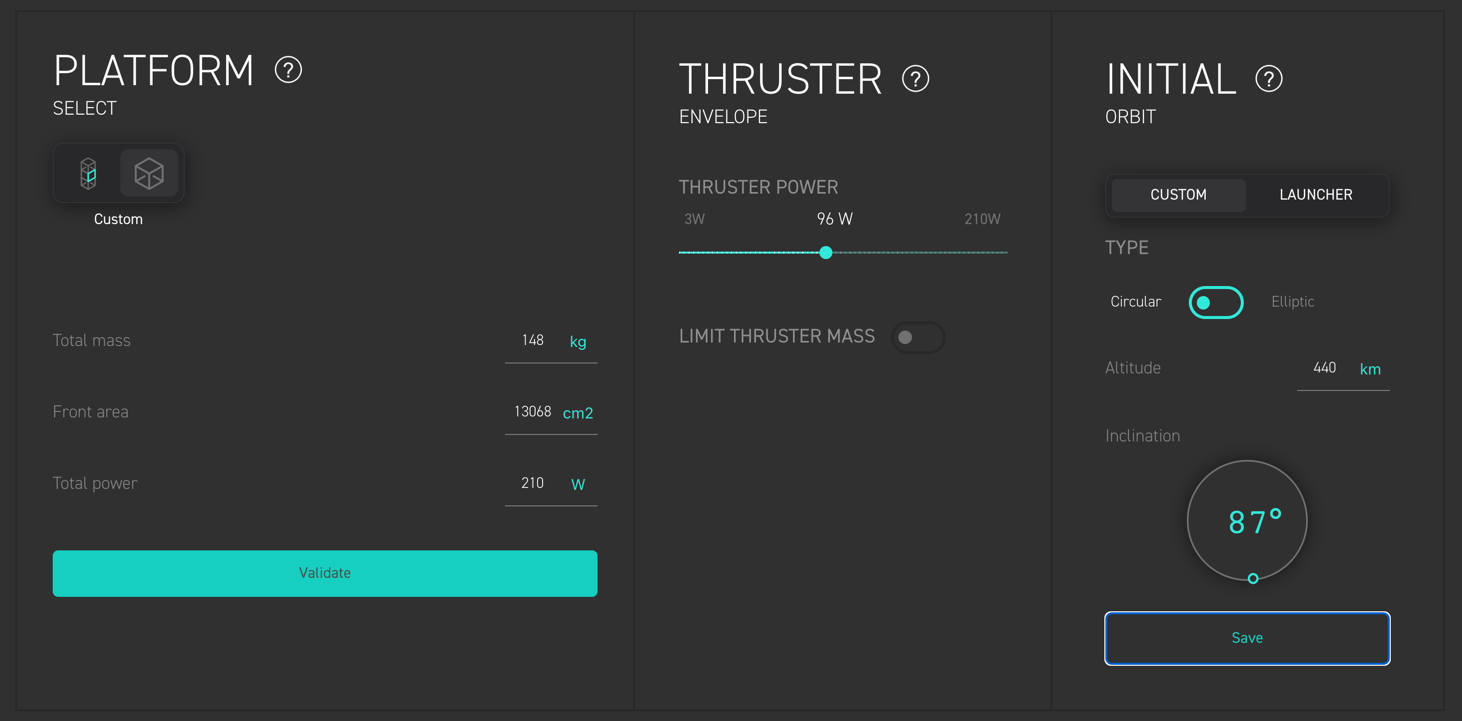
The next step is to simulate the orbital maneuvers. As specified above, the mission can be broken down sequentially into an orbit phasing for co-planar slot placement, an orbit raising for deployment to the operational altitude, and, finally, a deorbiting maneuver for decommissioning after operation. Note that in the realistic case, OneWeb performs both phasing and orbit raising in parallel; in addition, the deorbiting strategy is undisclosed and unproven by OneWeb and thus some assumptions are made on the characteristics of this maneuver.
Orbit Phasing
In the Maneuver Scenario view in GO™, we select “Orbit phasing” for the first maneuver type and then set a 180º true anomaly shift. We toggle ON the RAAN shift compensation since the semi-major axis change for phasing generates a small relative RAAN difference, which can be balanced by adding a small out-of-plane thrust component, at the expense of slightly larger propellant consumption and longer maneuver times; since the maneuver simulates the worst case True Anomaly change in a single plane phasing of a constellation, the RAAN shift compensation would be necessary to ensure the correct geometry of said plane.
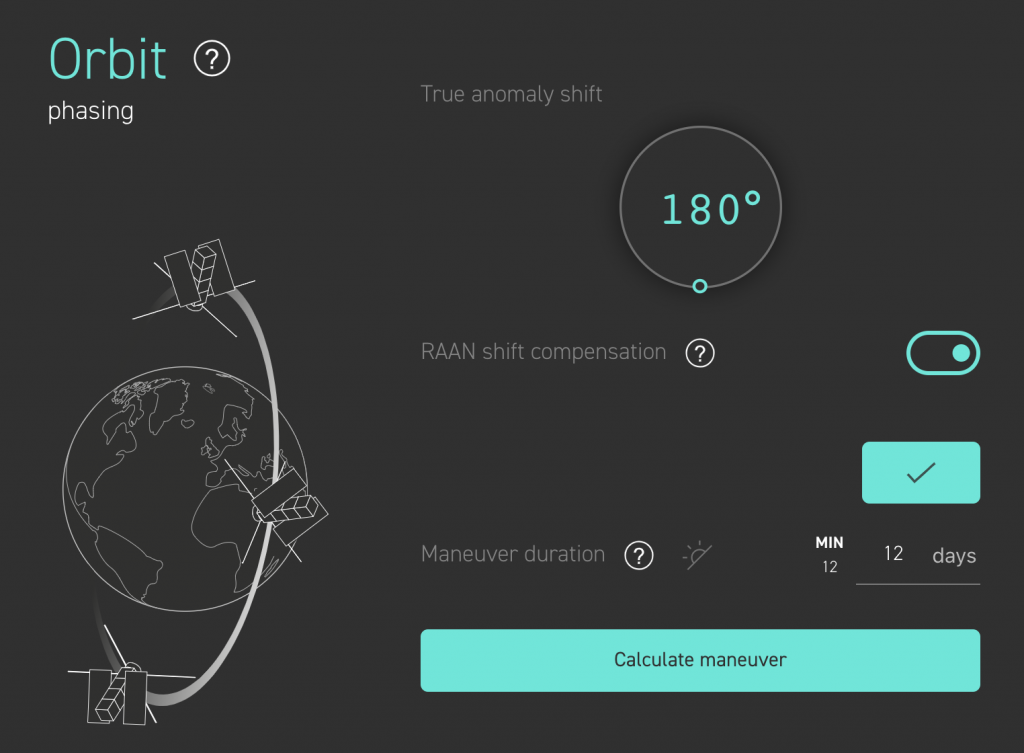
Once these values are selected, the minimum duration is calculated automatically by GO™, for the shortest physically possible maneuver or for the shortest maneuver allowed by the remaining propellant. We selected the shortest duration in this scenario, but the value might be modified to allow for longer maneuvers, at a lower expense in terms of propellant consumption. Clicking on “Calculate maneuver” shows the results and orbital element time profiles during the maneuver.
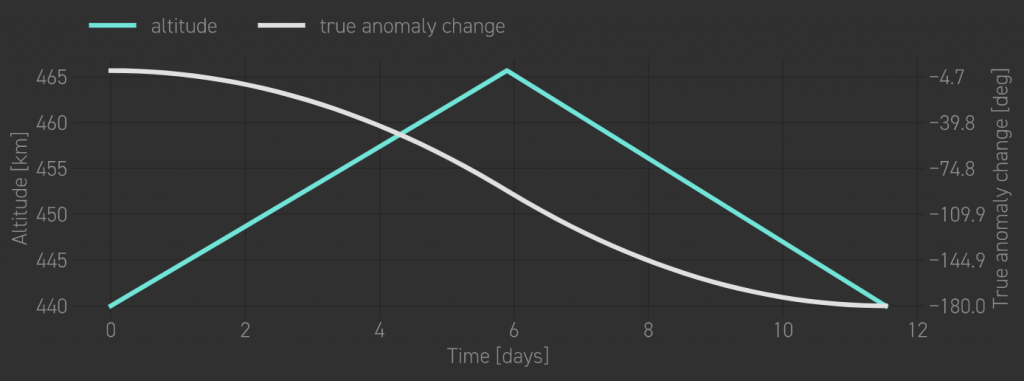
In the results shown in Figure 5, the maneuver for the 180º true anomaly change takes slightly less than 12 days and uses only 262.6 grams of propellant. Note that this is the worst case scenario: the rest of satellites in the constellation would require shorter maneuvers and less propellant.
Orbit transfer
The next step is to set the orbit transfer to the operational altitude. The initial configuration is fairly simple; it is possible to choose between elliptic and circular final orbits, the target altitude, and finally the desired inclination. As for the previous maneuver, the minimum duration was selected. The target altitude was set to the previously specified altitude, and the inclination was set to 88º, which is the closest integer value to the maneuver performed by OneWeb in Figure 2; future updates of GO™ will allow for decimal values of inclination, permitting further refinement of the calculations.
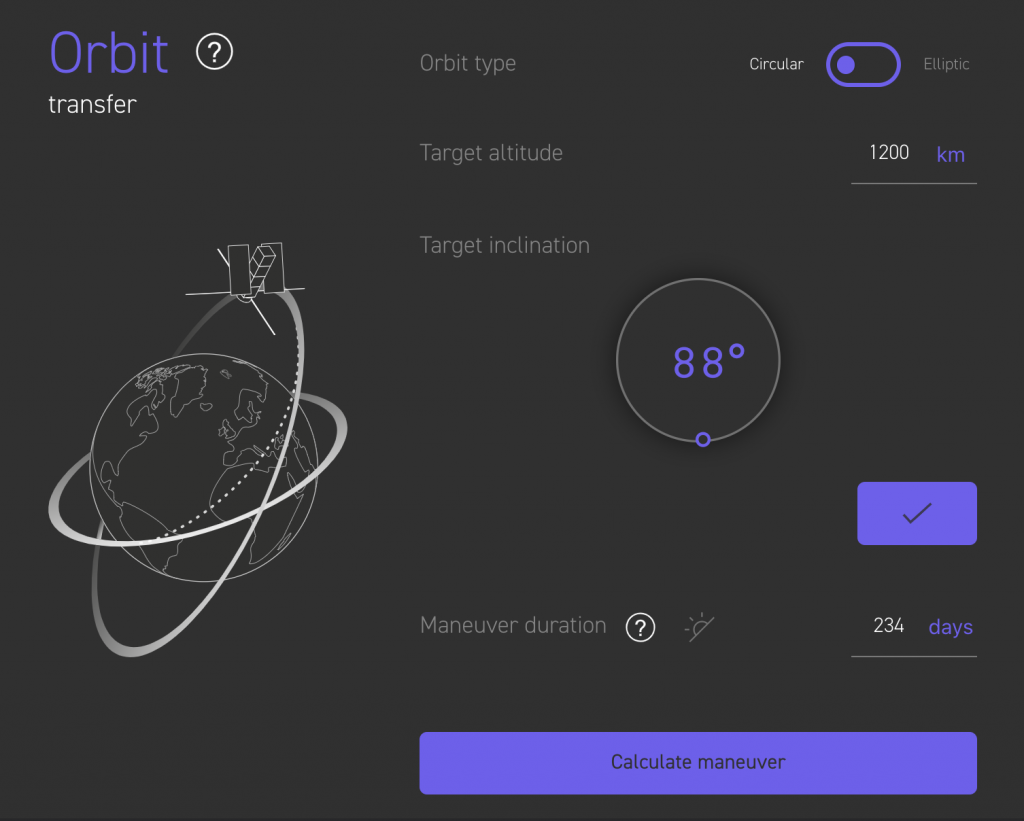
Figure 7 shows the results of two consecutive maneuvers, with the orbit raising taking 150 days and the inclination change lasting 84 days, for a total maneuver duration of 234 days. Note that the actual inclination change is from 87.4º to 87.9º, which could be performed in about half the time, 42 days, resulting in a total transfer duration of 192 days and thus what is shown here is considered a conservative overestimation. The propellant mass consumed is about 5.3 kg (vs 4.3 kg for the real inclination change). Results could be further improved by performing a combined maneuver, varying both elements at the same time, which will be possible in future GO™ releases.
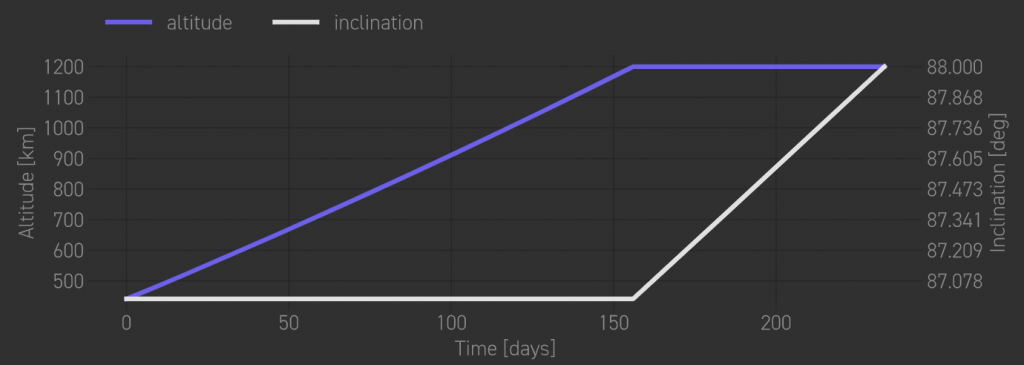
Deorbit
Finally, the satellite is planned to be decommissioned. In the Deorbit maneuver, the minimum and maximum durations are automatically computed. The only input is the maximum number of days required for the satellite’s reentry. In this case, the fastest deorbit would take about 188 days, but a maximum of 1,825 days (5 years) was assumed in order to reduce the amount of propellant while still decommissioning in a relatively short timespan.
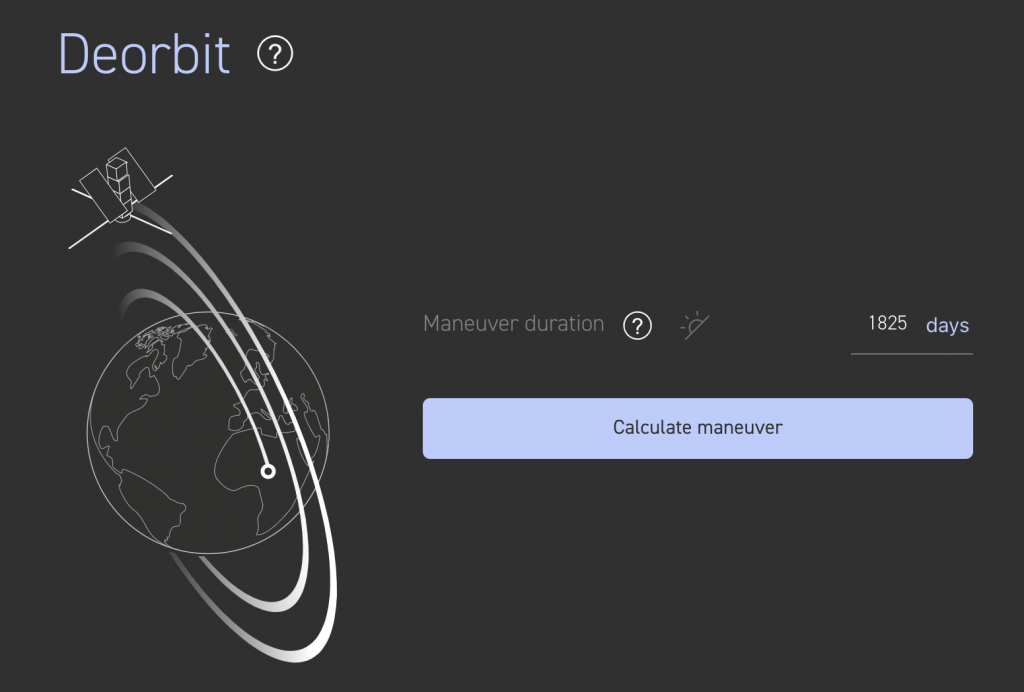
The resulting maneuver is shown in Figure 9, despite the input being 1825 days, the maximum duration of the deorbit from 1,200 km to 100 km is 1,294 days by using the minimum thrust possible (corresponding to 5W of power and only two emitters being actuated), consuming a total of 3.8 kg of propellant; a future release of GO™ will allow for tuning the duty cycle of the thruster to allow for longer maneuvers, even at minimum thrust. This maneuver potentially overestimates what will eventually be shown to be the deorbiting strategy of OneWeb, but since no existing reference exists, we propose it as a valid option.
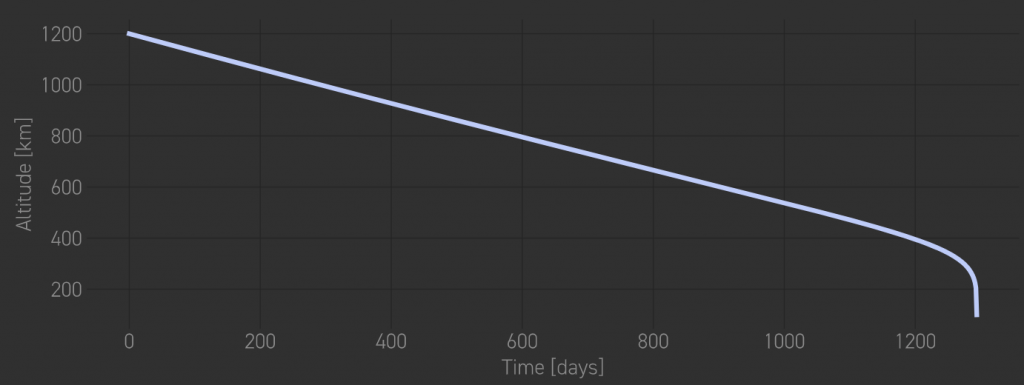
CONCLUSIONS
The aggregate results of the mission are shown in Figure 10; The total thrusting time is about 1538 days, with the deorbit maneuver accounting for the majority of that time; the total ΔV, however, is around 1km/s, where 60% is allotted to the orbit raising maneuver; again, the deorbiting maneuver is potentially overestimated here compared to what would be a realistic case. The total propellant consumption is around 9 kg, representing around 6% of the platform mass. The deployment to the actual operational orbit is achieved after the first 204 days using the ATHENA™ propulsion system (for the realistic inclination change of 0.5º); in comparison, SPT-50M achieves the same maneuver in about 160 days. The quicker maneuver is a result of the higher thrust-to-power of the Hall-thruster, nonetheless, the propellant savings for the referenced maneuver (orbit raising) are around 33%: the SPT-50M needed approximately 7.9kg of Xenon, whereas ATHENA™ consumed only 5.3kg of propellant.
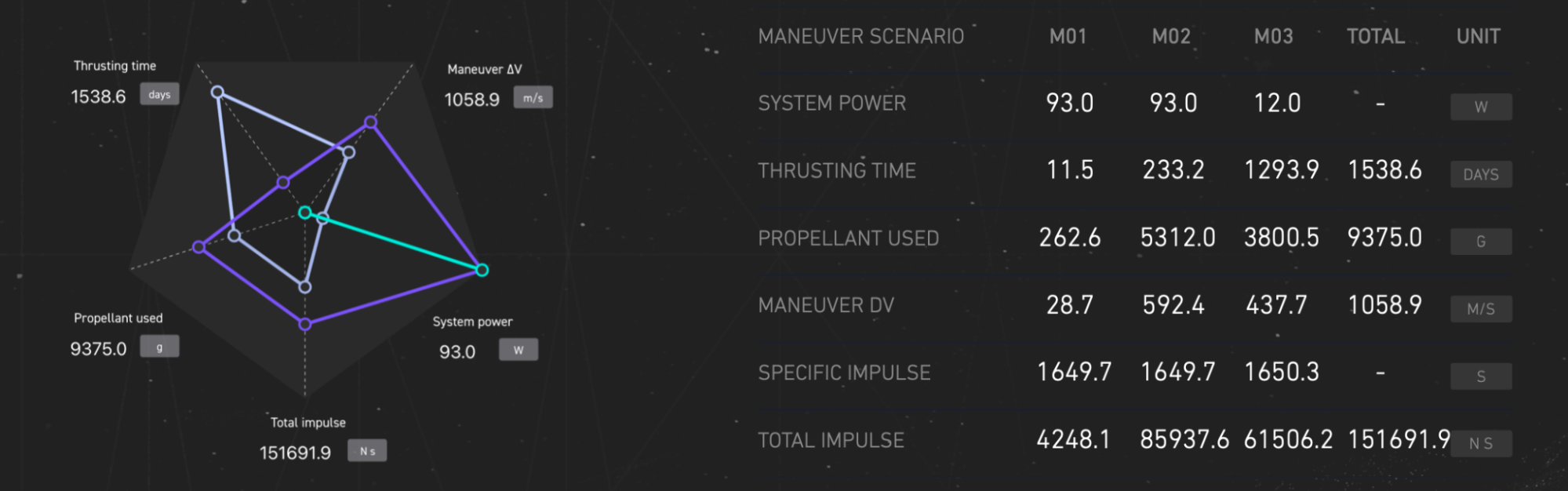
Note that the orbit raising maneuver can be optimized by performing a combined maneuver during the orbit raising, as mentioned before, and that the total propellant use could be much reduced by extending the maximum duration of the decommissioning maneuver. These propellant savings might very well appear negligible, but the comparison in propellant costs reveals an added benefit of electrospray thrusters: Xenon is currently sold for as much as $3000 per kg, whereas ionic liquid propellants can be purchased for $1000 per kg. Only the orbit raising maneuver would have saved about $8M when considering the entire existing constellation of 428 satellites, if considering the entire constellation planned the savings go up!
By providing similar performances, ATHENA™ is capable of reducing the propellant mass used by more than 30%, and lowering the cost by around 60%. Besides, ATHENA™ has proven to be a strong player for its future implementation in small satellites. Furthermore, ienai SPACE can offer additional customization capabilities for the ATHENA™ thrusters, tuning the form factor in a way that would be more agreeable with the existing subsystems in the spacecraft, without requiring extensive re-engineering.
→Download the summary for the OneWeb mission!
→Register for GO™ and create your custom thrusters!